Last updated on January 3rd, 2025 at 10:17 am
At Approved Sheet Metal, our sheet metal fabrication experts fabricate brackets for product developers across the country that design for a broad range of commercial, and military applications.
In this guide, we share some background on the processes we use to manufacture custom sheet metal brackets, explore different bracket types, and share tips to help you design the ideal custom brackets for your applications.
Table of Contents
- 1 What Are Sheet Metal Brackets?
- 2 How Our Sheet Metal Fabrication Shop Fabricates Brackets
- 3 Common Bracket Types
- 4 Design Considerations for Custom Brackets
- 5 Recommended Default Sheet Metal Tolerances
- 6 Sheet Metal Bracket Design FAQ
- 6.0.1 What are sheet metal brackets, and what purposes do they serve?
- 6.0.2 What materials are commonly used for fabricating brackets?
- 6.0.3 What fabrication processes are employed for manufacturing brackets?
- 6.0.4 What are the most common types of sheet metal brackets?
- 6.0.5 What design considerations should one keep in mind when creating custom brackets?
What Are Sheet Metal Brackets?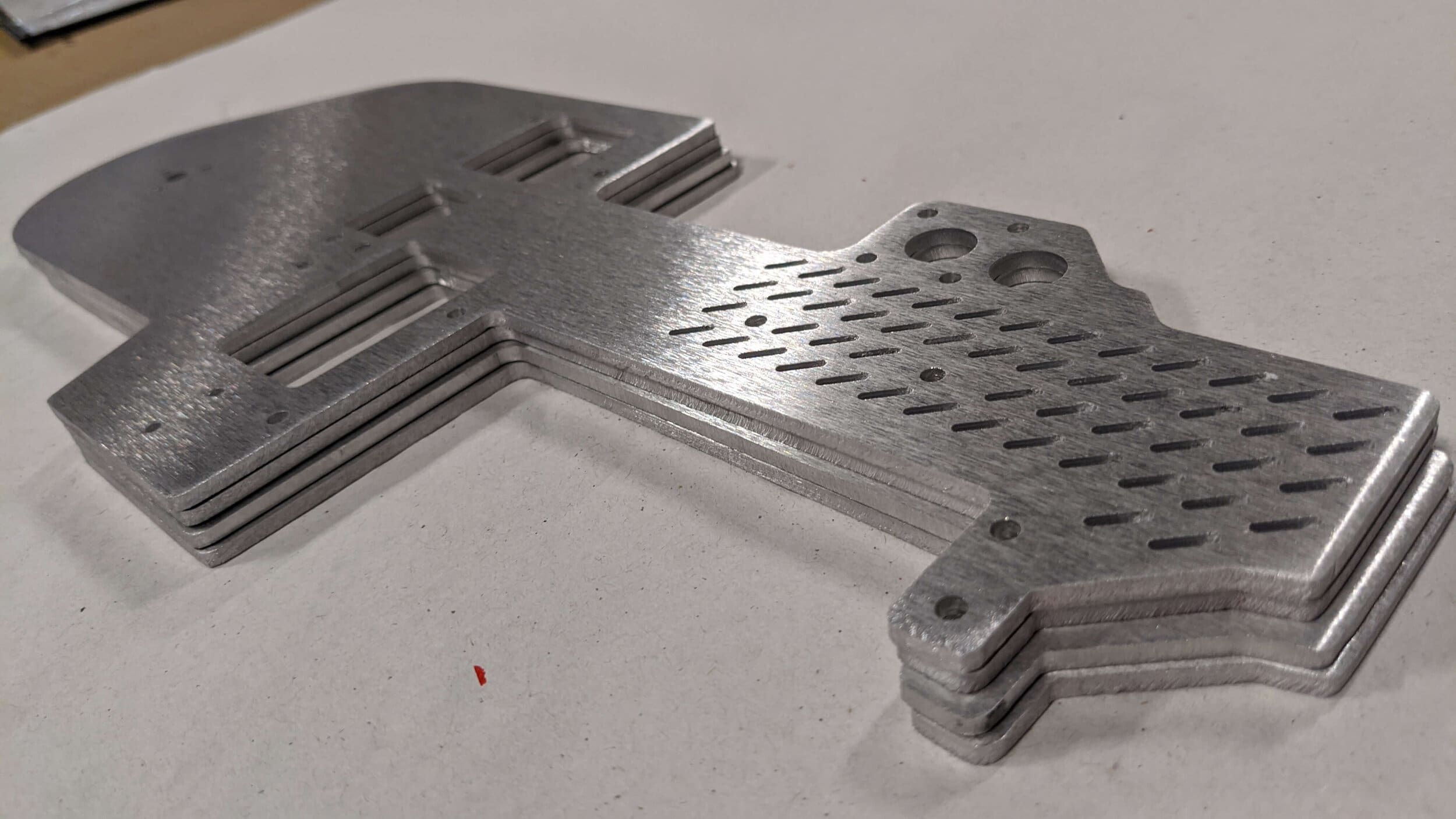
Brackets are intermediate components that attach one object to another (e.g., a shelf to a wall), align parts within an enclosure, or fortify a part by supplying extra structural support. Depending on its type, a bracket is either mounted with hardware or welded inside a sheet metal part.
Brackets are typically functional in nature but can be used for decorative purposes.
Standard Bracket Materials
We fabricate brackets from a variety of materials, including:
How Our Sheet Metal Fabrication Shop Fabricates Brackets
Sheet metal fabrication is one of the most simple and cost-effective ways to create brackets. At ASM, we use a combination of fabrication methods to manufacture exceptionally strong, durable brackets for our customers.
Cutting
First, we use our laser cutter to cut a flat piece of sheet metal to the specified size.
Forming
We then bend the cut metal piece at one or more angles, typically using a press brake, to produce the desired shape.
Punching
For brackets that will be mounted, we leverage our punch forming capabilities to create holes for mounting hardware.
Welding
Brackets designed to fortify or stiffen metal are welded into place rather than fastened.
Common Bracket Types
No matter which type of bracket you need, our sheet metal fab shop can make it. Here are the standard bracket types we fabricate:
L brackets
The most common bracket type, an L bracket has a single bend that lends it an L shape. L brackets are most often bent at a 90-degree angle but can be bent to angles up to 120 degrees.
Z brackets
Z brackets have two bends that create parallel flanges pointing in opposite directions, making a Z or double L shape. These brackets are often used to anchor parts at different levels within an enclosure or prop up parts that require air flow beneath them.
U-channel brackets
U-channel brackets have two bends at facing angles, creating a U shape. Typically much longer than L or Z brackets, they require multiple holes for mounting hardware. These brackets are ideal for mounting parallel surfaces together.
Hat channel brackets
These top hat-shaped brackets are welded inside parts made of weaker metal to keep them from collapsing inward (e.g., inside metal doors).
Gusset brackets
Like hat brackets, gusset brackets are welded inside metal parts for added fortification. Often triangular in shape, they are commonly used in architectural applications, such as bridges.
Design Considerations for Custom Brackets
Creating brackets is generally straightforward, but there are a few factors to keep in mind when designing these parts to ensure optimal results.
Material strength
Always consider the load your bracket will need to support. Will the material you’ve chosen be strong enough to accommodate it? If you need help selecting the right material for your application, our team is happy to help!
Flange proportions
For U-channel and hat-channel brackets, specific flange proportions must be maintained to prevent the part from slipping out of place in the press brake.
Design forming flanges shorter than the base flange to ensure your bracket can be pressed properly. If these proportions are reversed, we may need to acquire custom tooling to create your part, which will increase your cost.
ASM’s perfect fit flange formula can help you design foolproof flanges for your bracket!
Hole placement
One of the most common questions we get from customers designing brackets is where to place bracketry holes in relation to bends. When possible, add holes a safe distance from bends to simplify punching operations, which can help optimize costs and lead times.
Finishing Options for Custom Sheet Metal Fabricated Brackets
- Powder Coating
- Overview: Powder coating involves applying a dry powder to the bracket surface and then curing it under heat to form a durable, decorative finish.
- Benefits:
- High resistance to corrosion, UV exposure, and wear.
- Wide variety of colors and textures for aesthetic customization.
- Environmentally friendly with minimal waste.
- Applications: Ideal for brackets exposed to harsh environments or requiring a decorative touch, such as outdoor fixtures or furniture components.
- Anodizing (For Aluminum Brackets)
- Overview: Anodizing enhances the natural oxide layer on aluminum surfaces, improving durability and corrosion resistance.
- Benefits:
- Excellent protection against corrosion and wear.
- Offers color options through dyeing processes.
- Lightweight while maintaining a sleek metallic look.
- Applications: Common for brackets in consumer electronics, aerospace, and automotive industries.
- Plating (e.g., Zinc, Nickel, or Chrome)
- Overview: Electroplating adds a thin metallic layer to brackets, enhancing both appearance and resistance to rust or wear.
- Benefits:
- Superior corrosion resistance.
- Reflective, polished appearance.
- Cost-effective for small to medium production runs.
- Applications: Often used for brackets in decorative, medical, or electrical applications.
- Painting
- Overview: Wet painting provides a versatile finishing option, particularly for unique colors or textures not achievable with powder coating.
- Benefits:
- Flexible in terms of color matching and application.
- Can be used on both metal and composite brackets.
- Less equipment-intensive than powder coating.
- Applications: Suitable for low-production runs or brackets used in interior environments.
- Passivation (For Stainless Steel Brackets)
- Overview: Passivation involves treating stainless steel brackets with an acid solution to remove contaminants and enhance their natural corrosion resistance.
- Benefits:
- Preserves the natural appearance of stainless steel.
- Excellent protection against rust and oxidation.
- Applications: Common in brackets used for medical devices, food processing equipment, and marine applications.
- Polishing
- Overview: Mechanical or chemical polishing creates a smooth and reflective surface on brackets, improving both appearance and functionality.
- Benefits:
- Eliminates surface imperfections like scratches or burrs.
- Creates a mirror-like finish for high-end applications.
- Applications: Frequently used for brackets in decorative or precision equipment.
Got questions about your bracket design? Ask our team, or better yet, request a design review!
Sheet Metal Bracket Design FAQ
Sheet metal brackets are intermediary components used to connect, align, or reinforce objects. They can attach objects together, provide structural support, or align parts within an enclosure. Brackets can be functional or serve decorative purposes.
Approved Sheet Metal fabricates brackets from various materials, including cold rolled steel, 5052 aluminum, and stainless steel, offering durability and strength across different applications.
ASM utilizes multiple fabrication methods. They employ laser cutting to shape the metal, press brakes for bending, punching for creating mounting holes, and welding for fortifying brackets within metal parts.
ASM fabricates a range of bracket types, including L brackets (with a single bend), Z brackets (with two bends creating parallel flanges), U-channel brackets (having a U shape), hat channel brackets (top-hat-shaped, used to prevent collapsing), and gusset brackets (triangular, for added fortification).
Designing custom brackets involves considering factors like material strength relative to the load, maintaining specific flange proportions for U-channel and hat-channel brackets, and strategically placing holes relative to bends to simplify punching operations, optimizing cost and lead times. ASM offers guidance on material selection and optimal design practices for bracket fabrication.