Last updated on April 1st, 2025 at 09:28 am
Sheet metal finishing is an important final step in the custom sheet metal fabrication process. Powder coating and wet paint are two of the most common finishing services customers request.
Here, we’ll briefly explore each service and provide expert input on selecting the one that best fits your needs.
Table of Contents
- 1 What Is Powder Coating?
- 2 What Is Wet Paint?
- 3 Cost & Production Efficiency Analysis
- 4 Cost & Production Efficiency Analysis
- 5 Get Custom Sheet Metal Fabrication Finishing Services
- 6 6 Tips for Designing Powder Coated Sheet Metal Parts
- 7 Sheet Metal Fabrication Powder Coat or Wet Paint FAQ
- 7.0.1 What is the primary difference between powder coating and wet paint in sheet metal finishing?
- 7.0.2 How do I ensure the correct color and gloss level when opting for powder coating?
- 7.0.3 What are the advantages of powder coating over wet paint?
- 7.0.4 When might wet paint be a more suitable choice over powder coating?
- 7.0.5 How does Approved Sheet Metal assist in selecting the ideal finishing method for custom sheet metal parts?
What Is Powder Coating?
Powder coating is a process in which thermoplastic powder is electrostatically charged and sprayed onto a part with an applicator gun. The charged powder adheres to the part, which is then transferred to an oven and cured at a temperature of 400-450 degrees Fahrenheit.
Powder coat is available in a vast array of colors and textures. When placing an order for powder coating services, it’s important to provide the exact RAL code for the powder coat brand you wish to use. This code tells your sheet metal fabricator the precise color and gloss type.
While a callout such as “powder coat black” may seem straightforward, there are actually dozens of different “blacks” that vary considerably in color and gloss level. This variability can be especially problematic if you’re trying to match the color of an existing part.
If you need help selecting the right powder coat color for your parts, just ask! As a sheet metal fabricator with in-house powder coating services, we’re happy to help you plan for an excellent outcome. Get six tips for designing powder coated sheet metal parts here!
Benefits of powder coating
Although the curing time depends on the powder type, powder coating is always a faster option than wet paint, which requires primer and paint applications that both must air dry. Because powder coating is more efficient, it is typically less expensive than wet paint—especially at ASM, where we provide powder coating services under our own roof.
Almost any material can be powder coated, and powder coating is well suited to a variety of applications. Whether your part will be used indoors or outdoors, kept relatively protected or exposed to harsh conditions, powder coating provides a highly protective and attractive finish.
Limitations of powder coating 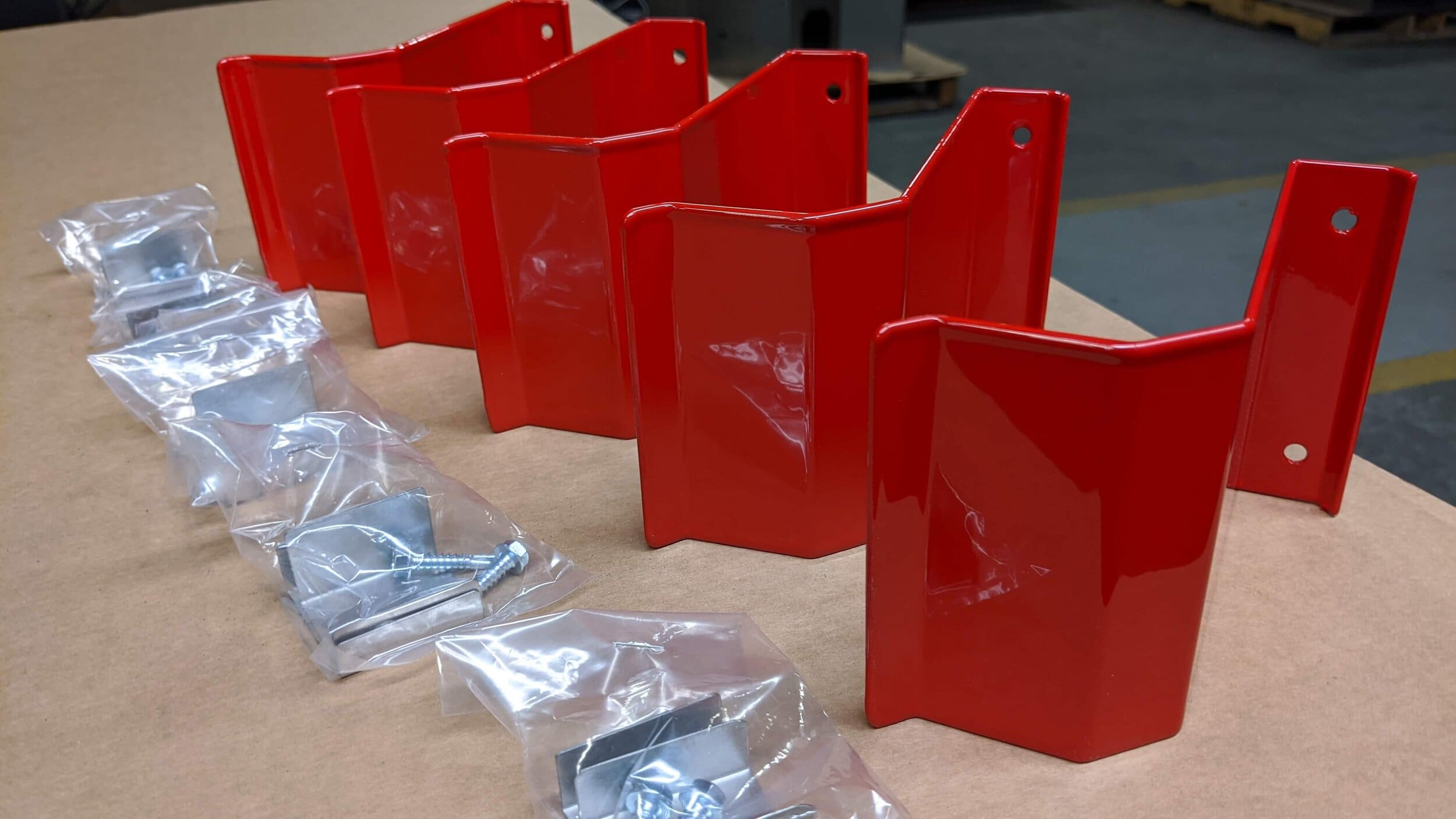
Powder coating does not perform well on parts requiring multiple colors, such as many legacy military parts. When applying more than one powder coat color to a part, a portion of the part must be masked during application. When exposed to the heat of the curing oven, the masking adhesive often leaves residue on the part that is difficult to remove, resulting in an unsatisfactory finish.
It’s also important to note that certain hardware types, such as nylon inserts, will melt during curing and thus should be inserted only after the powder coating process is complete. It’s your sheet metal fabricator’s responsibility to look for these components in your part design and take the proper precautions to prevent negative outcomes.
What Is Wet Paint?
Wet paint is applied with a liquid spray gun and, like powder coat, comes in a wide range of colors and sheens that should be identified with a RAL code. The wet paint process has multiple application steps. A primer must first be applied, followed by at least one coat of paint.
Benefits of wet paint
Wet paint provides a durable, attractive coat for parts across a wide range of materials and applications. It's an excellent choice for multi-color parts, as the wet paint process introduces no risk of adhesive residue.
Limitations of wet paint
Because wet painted parts must air dry between primer and paint applications, the process is generally more time-consuming and expensive. When time or budget are limited, powder coating is typically the better choice.
Cost & Production Efficiency Analysis
When selecting between powder coating and wet paint for sheet metal parts, it's essential to consider not only the immediate cost of each finishing process but also the long-term production efficiency and overall cost-effectiveness. Here's a deeper look into how both options stack up from a financial and operational perspective:
1. Initial Costs
Powder Coating: While the equipment required for powder coating (such as the spray guns and curing ovens) can represent a higher initial investment, the process itself tends to be more cost-effective in the long run, particularly for high-volume orders. The main cost considerations include the powder itself, energy consumption during curing, and labor. Because the process doesn't require primers or additional drying time, labor costs and material handling are reduced.
Wet Paint: Wet painting requires more manual intervention, as multiple coats of primer and paint must be applied and allowed to dry, resulting in a more time-intensive process. This increases the labor cost per part. Additionally, the need for ventilation systems to handle solvent fumes and the use of hazardous chemicals can incur regulatory compliance costs and environmental fees. Equipment costs may also be lower, but the ongoing need for consumables (paint, primer, thinner) adds to the overall price.
Cost & Production Efficiency Analysis
When selecting between powder coating and wet paint for sheet metal parts, it's essential to consider not only the immediate cost of each finishing process but also the long-term production efficiency and overall cost-effectiveness. Here's a deeper look into how both options stack up from a financial and operational perspective:
1. Initial Costs
Powder Coating: While the equipment required for powder coating (such as the spray guns and curing ovens) can represent a higher initial investment, the process itself tends to be more cost-effective in the long run, particularly for high-volume orders. The main cost considerations include the powder itself, energy consumption during curing, and labor. Because the process doesn't require primers or additional drying time, labor costs and material handling are reduced.
Wet Paint: Wet painting requires more manual intervention, as multiple coats of primer and paint must be applied and allowed to dry, resulting in a more time-intensive process. This increases the labor cost per part. Additionally, the need for ventilation systems to handle solvent fumes and the use of hazardous chemicals can incur regulatory compliance costs and environmental fees. Equipment costs may also be lower, but the ongoing need for consumables (paint, primer, thinner) adds to the overall price.
2. Production Efficiency
Powder Coating: Powder coating is typically faster than wet paint, especially when dealing with large batches. The powder is applied in a single step, then baked in a curing oven, which generally takes between 10-20 minutes depending on the material and part size. Because the curing process happens quickly, this significantly reduces overall turnaround time. Additionally, powder coating overspray can be collected and reused, improving material efficiency and reducing waste.
Wet Paint: Wet painting requires more steps, including applying a primer, allowing it to dry, applying paint, and allowing it to dry again. This extended timeline can delay production, especially for parts with intricate designs that require more detailed masking or finishing. Drying time also creates bottlenecks in the production line, making it less ideal for high-volume or time-sensitive orders.
3. Long-Term Cost Considerations
Powder Coating: The durability and resilience of powder coating often mean that parts will require less maintenance and reapplication over time. The process creates a thicker and more robust finish, making parts more resistant to scratches, wear, and environmental damage. This translates into fewer repairs or touch-ups down the line, ultimately saving costs in the long term.
Wet Paint: Wet paint can wear down more quickly, especially in harsh environments, requiring touch-ups or complete reapplications over time. For parts exposed to corrosive environments or heavy wear, wet paint may not offer the longevity of powder coating, leading to increased maintenance and operational costs over the product's lifecycle.
4. Volume Considerations
Powder Coating: Powder coating is especially cost-efficient for high-volume production. The ability to cure large batches of parts simultaneously in an oven allows manufacturers to process many pieces in a shorter time frame. This is particularly beneficial for industries that require consistent, high-quality finishes on mass-produced components. The efficiency of the process makes it more economical for large-scale projects, offsetting the initial equipment costs over time.
Wet Paint: Wet paint is better suited for smaller runs or custom orders where multiple colors or complex finishes are needed. While the process is slower, the flexibility of wet paint allows for more customization. However, in high-volume production environments, the process becomes more labor-intensive and less efficient.
5. Material Waste
Powder Coating: One of the significant advantages of powder coating is its reduced material waste. Powder overspray is easily recovered and reused, making it a more sustainable and cost-effective choice. In fact, the transfer efficiency of powder coating can be as high as 98%, meaning nearly all the material that is sprayed onto the part is used effectively. This reduces both material costs and environmental impact.
Wet Paint: Wet paint tends to generate more waste, as the excess paint that is sprayed onto the part and not absorbed by the substrate is often discarded. Additionally, the use of solvents for cleanup can result in higher waste disposal costs. The transfer efficiency of wet paint is typically lower than powder coating, which can lead to higher material costs and waste.
Get Custom Sheet Metal Fabrication Finishing Services
At ASM, we’re committed to helping you attain the ideal finish for your parts. Whether that means powder coating your parts in one of our in-house booths or outsourcing wet paint services to one of our trusted vendors, we’re the sheet metal fabricator you can count on to deliver exceptional results.
Request a quote for our custom sheet metal fabrication services!
Sheet Metal Fabrication Powder Coat or Wet Paint FAQ
Powder coating involves electrostatically spraying thermoplastic powder onto the part, which is then cured in an oven. Wet paint, on the other hand, involves applying liquid paint with a spray gun after applying a primer.
When requesting powder coating, providing the exact RAL code for your preferred color and gloss type is crucial. This detailed code ensures precision in color selection, especially considering the wide variability among seemingly similar shades.
Powder coating is typically faster and more cost-effective as it requires less curing time compared to wet paint, which demands drying time for both primer and paint applications. It's versatile and provides excellent protection for various applications and environmental conditions.
Wet paint is preferable for multi-color parts without the risk of adhesive residue. However, it generally takes more time and can be costlier due to the multiple application steps. When time or budget constraints exist, powder coating often becomes the better option.
At ASM, we're dedicated to helping you achieve the perfect finish for your parts. Whether it's powder coating within our facilities or outsourcing wet paint services, we guide you through the selection process to ensure exceptional results aligning with your specific needs.