Last updated on May 22nd, 2025 at 10:19 am
True or false: Aluminum is resistant to rust and decay.
The answer might surprise you. While pure aluminum is 100% corrosion-resistant; aluminum alloys are not. And pure aluminum is expensive, so unless you’re NASA, you’re looking at alloys for most or all of your parts.
So how do you protect your parts from corrosion?
Table of Contents
- 1 Don’t Just Anodize, Color-Anodize!
- 2 Why Color-Anodize?
- 3 Types of Color Anodizing
- 4 When to Color-Anodize
- 5 Recommended Default Sheet Metal Tolerances
- 6 Color Anodize Sheet Metal Part FAQ
- 6.0.1 Is aluminum resistant to rust and decay?
- 6.0.2 What is the purpose of anodizing aluminum?
- 6.0.3 How does color-anodizing differ from standard anodizing, and why is it used?
- 6.0.4 What are some examples of when to use color-anodizing for aluminum parts?
- 6.0.5 What colors are available for color-anodizing aluminum parts?
Don’t Just Anodize, Color-Anodize!
Anodizing, the process of adding a thicker, oxide layer over aluminum to protect it from rust and wear, has been around for a long time. Anodizing not only protects aluminum alloys from weather and the elements, it can also provide electrical insulation. It’s especially important for parts that are routinely or constantly submerged in water.
When you anodize, you also get a better-looking product: it gives aluminum a smoother, scratch-free surface with no nicks or bumps.
At Approved Sheet Metal, we pride ourselves on precision sheet metal fabrication, but we like to have a little fun, too. And what better way to dress up your next sheet metal prototype or part than with color-anodizing?
The oxide layer created during anodization is porous, which allows for the introduction of color. For you creative types out there, that means aluminum parts can be more exciting than your standard metal, black, or clear finishes.
Why Color-Anodize?
Honestly--why not?
There’s a huge range of colors available for color anodizing. Make your next part stand out with one of these hues:
Teal, Brown, Gold, Grey, Pink, Blue, Green, Red, Orange, Purple
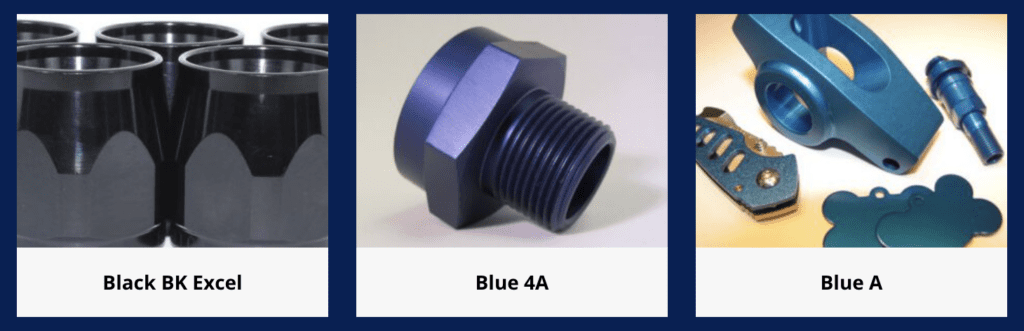
Types of Color Anodizing
Not all color anodizing processes are created equal. Different types of anodizing offer varying degrees of durability, color vibrancy, and suitability for technical applications. For mechanical engineers, understanding these distinctions is critical when specifying finishes that serve both aesthetic and functional roles.
Type I – Chromic Acid Anodizing (Rarely Colorized)
- Oxide Thickness: ~0.00002" to 0.0001"
- Key Traits: Thin, less porous layer; ideal for tight tolerance applications.
- Coloring Limitations: Typically not dyed due to its limited porosity and pale gray appearance.
- Common Uses: Aerospace applications where fatigue resistance and dimensional precision are critical.
Type II – Sulfuric Acid Anodizing (Standard Color Anodizing)
- Oxide Thickness: ~0.00007" to 0.001"
- Key Traits: Moderate hardness and porosity, making it ideal for vibrant dye absorption.
- Color Capabilities: Wide range of colors (red, blue, gold, green, black, etc.).
- Common Uses: Consumer electronics, medical devices, architectural panels, and general-purpose components.
Type III – Hard Coat Anodizing (Also Called Hard Anodizing)
- Oxide Thickness: ~0.0005" to 0.004"
- Key Traits: Extremely durable and wear-resistant; often used for high-friction or high-load applications.
- Color Capabilities: Limited due to the thickness and density of the oxide layer—typically black, gray, or dark bronze.
- Common Uses: Military hardware, industrial tooling, and components exposed to harsh environments.
When to Color-Anodize
Color anodize if you want your part to grab attention (if it’s part of an emergency feature, for example), coordinate different pieces for ease of assembly, or simply stand out.
It’s perfect for products like:
- Aluminum artwork
- Aluminum signages
- Communication tools
- Automotive parts
- Medical devices
- Educational instruments
- Dock components
Add a pop of color to your next aluminum part while protecting it, too.
Request a quote for your next sheet metal fabrication project—and don’t forget to ask about color-anodizing!
Color Anodize Sheet Metal Part FAQ
The answer is both true and false. Pure aluminum is 100% corrosion-resistant, but most parts are made from aluminum alloys that are not. To protect aluminum alloys from corrosion, additional measures are necessary.
Anodizing is a process that adds a thicker oxide layer to aluminum to protect it from rust and wear. It is also used to provide electrical insulation and is particularly important for parts exposed to water.
Color-anodizing is a variation of anodizing that introduces color to the porous oxide layer. It is used to enhance the appearance of aluminum parts by offering a range of colors, making them more visually appealing and suitable for various applications.
Color-anodizing is ideal for parts that need to grab attention, coordinate with other pieces for assembly, or simply stand out. It's commonly used for aluminum artwork, signages, communication tools, automotive parts, medical devices, educational instruments, and dock components.
A wide range of colors is available for color-anodizing, including teal, brown, gold, grey, pink, blue, green, red, orange, and purple. These colors can add a pop of vibrancy to your aluminum parts while providing corrosion protection.