Last updated on January 14th, 2025 at 11:51 am
Bump-forming may be the best solution for rapid sheet metal fabrication.
Is it better to bump-form or use hard tooling?
If you’re manufacturing a new part, choosing the right metal bending technique can affect both cost and lead time. But to answer the question for your next project, you need to look at a few key factors.
Table of Contents
- 1 What bump forming is and how to leverage it in your design
- 2 Bump-Forming vs. Hard Tooling
- 3 Recommended Default Sheet Metal Tolerances
- 4 Sheet Metal Bump Forming FAQ
- 4.0.1 What is bump-forming, and how does it compare to hard tooling?
- 4.0.2 What are the advantages of bump-forming for sheet metal fabrication?
- 4.0.3 What are the downsides of bump-forming in sheet metal fabrication?
- 4.0.4 Can bump-forming be used for large sheet metal parts?
- 4.0.5 When is bump-forming the best solution for rapid sheet metal fabrication?
What bump forming is and how to leverage it in your design
Bump-forming, otherwise known as bump-bending, is a series of bends, usually done on a press brake, that allows you to create a cylindrical bend in your metal sheet. The radius pitch--the distance between two bumps--can be calculated to just a few degrees to achieve a smooth, precise result.
One job we recently completed was .062 505-H32 Alum with bends that were 63” long. Most fabricators can bump for parts that are less than 24” wide. As the length of the bend gets larger, the challenge in holding a straight uniform angle dramatically increases.
Upsides to bump-forming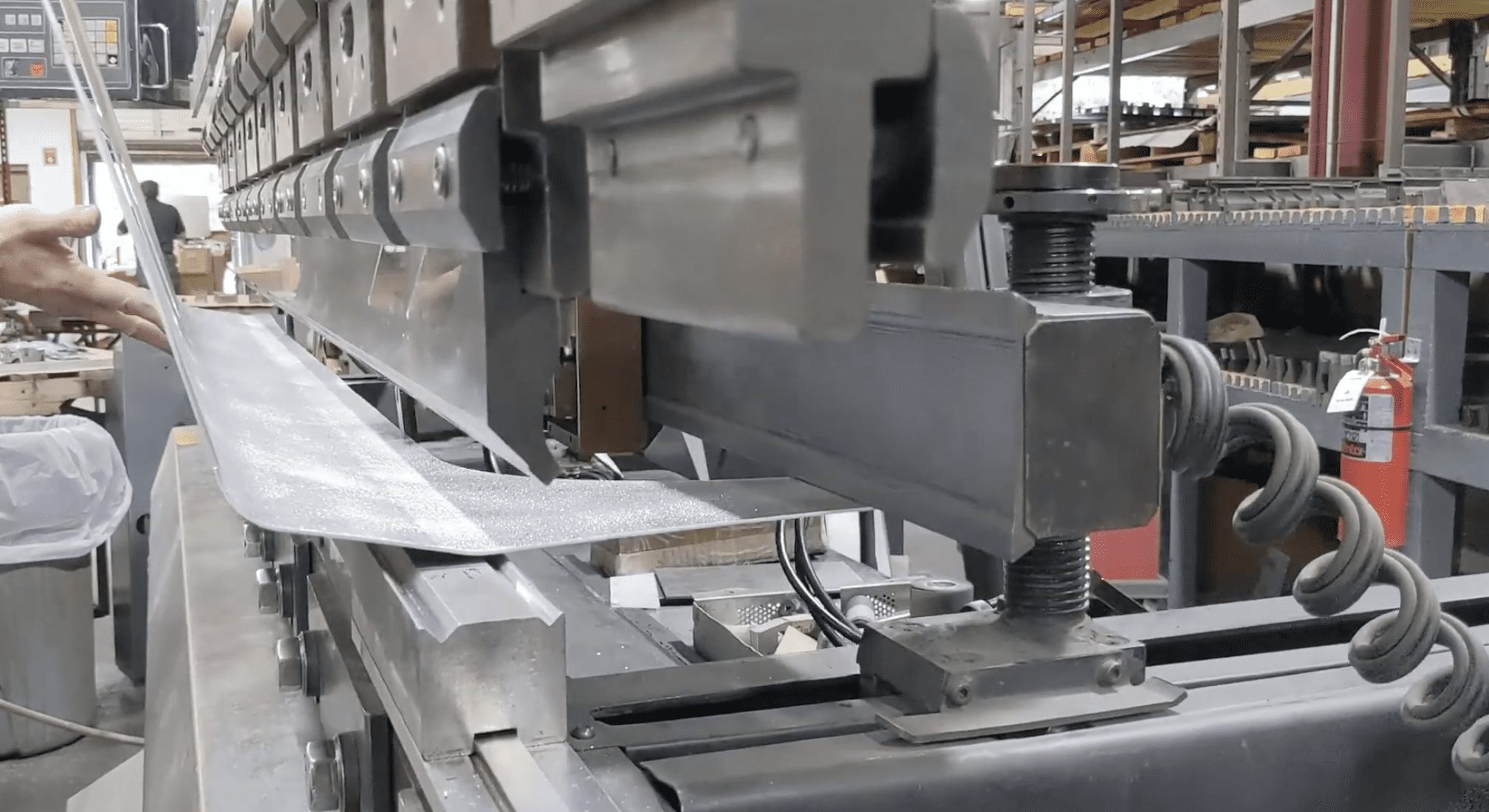
- No upfront cost. A plate roll can cost thousands of dollars and is an unnecessary expense if you’re not mass-producing!
- No waiting around. At ASM, we can bump form in-house rather than waiting for a special-ordered plate roll to arrive. That means we turn around your sheet metal parts faster.
- Precision. Bump-forming works well at smaller diameters. Calculating the exact degree you need for the bends can be time-consuming, and the process is slower than plate rolling. But for lower volume orders, it’s often more efficient in the long run.
Downsides to bump-forming
- Years of experience. 5-10 years of experience is required for these types of jobs.
- Engineering time. Samples should be made first to calculate the exact bend deduction.
- Templates. A template to check against is important; this takes more time in engineering and adds to the set up time for the entire job.
- Scrap parts. Bump-forming is a skill and it will require a few extra parts to dial the angles in.
- Skill. This is the most difficult task performed on a press brake.
Bump-Forming vs. Hard Tooling
Hard tooling is a must if you’re mass-producing, especially parts with large diameters that are cylindrical in shape. However, hard tooling may not be a solution for creating prototypes with unique specifications or for quick turnover in rapid prototyping. Due to an average wait time of 4-weeks the tool example below would have cost us $15.
Tips for Designers: Optimizing Your Design for Bump-Forming
Designing parts for bump-forming requires careful planning to ensure precision and efficiency. Here are some practical tips to make the most of this process:
- Understand Material Limits:
- Choose materials that can withstand multiple bends without cracking. Aluminum alloys and mild steels often perform better in bump-forming. Avoid materials with low ductility, as they may fracture during the process.
- Specify Bend Radii Clearly:
- Ensure that your design specifies achievable bend radii. Avoid excessively tight radii that may lead to visible ridges or compromise the structural integrity of the part.
- Account for Tolerances:
- Include tolerances in your design that reflect the slight variations inherent in bump-forming. While precision is achievable, it’s essential to allow for minor discrepancies, especially for long bends.
- Simplify Geometry:
- Aim for clean, simple curves whenever possible. Complicated geometries can increase setup time and the risk of inconsistencies during forming.
Contact us to learn about our full capabilities in metal fabrication!
Sheet Metal Bump Forming FAQ
Bump-forming is a metal bending technique that uses a series of bends to create a cylindrical bend in your metal sheet. It's often more efficient and cost-effective for low-volume orders or prototypes, while hard tooling is necessary for mass-producing parts with large diameters.
Bump-forming has several advantages, including no upfront cost, faster turnaround times, and precision for smaller diameters. It's also more efficient for lower volume orders, which can help minimize costs.
Bump-forming requires years of experience, engineering time, templates, and extra scrap parts to dial in the angles. It's also the most difficult task performed on a press brake, which means it may not be suitable for all fabrication projects.
Bump-forming works well for parts that are less than 24 inches wide, but the challenge of holding a straight uniform angle dramatically increases as the length of the bend gets larger. Therefore, it may not be the best solution for large sheet metal parts.
Bump-forming is the best solution for rapid sheet metal fabrication when working with prototypes or low-volume orders, aiming for precision, and looking to minimize costs. It's a cost-effective and efficient way to produce parts with smaller diameters without incurring the upfront cost of hard tooling.