Last updated on March 13th, 2025 at 10:46 am
At Approved Sheet Metal, we know many of our customers need their parts ASAP, so we’re always finding ways to speed up the rapid sheet metal fabrication timeline.
We’ve successfully implemented many time-saving initiatives in our shop, such as offering same-day shipping for flat laser-cut sheet metal parts. However, there are also steps customers can take to expedite their precision sheet metal fabrication projects—one of the easiest is to provide comprehensive drawings.
Table of Contents
- 1 5 Ways to Optimize Drawings for Precision Sheet Metal Fabrication Services
- 2 Digital File Formats & Model Sharing
- 3 Sheet Metal Design for Manufacturing
- 4 Sheet Metal Fabrication Drawings FAQ
- 4.0.1 Why is it important to list part numbers in addition to part names in sheet metal fabrication drawings?
- 4.0.2 How can providing the exact hardware name help expedite precision sheet metal fabrication?
- 4.0.3 Why should revision control details be documented in sheet metal fabrication projects?
- 4.0.4 Why is it important to indicate the grain direction in sheet metal fabrication prints?
- 4.0.5 How can providing powder coat instructions improve the precision of sheet metal fabrication?
5 Ways to Optimize Drawings for Precision Sheet Metal Fabrication Services
Follow these best practices next time you create a sheet metal fabrication drawing to help your shop turn the project around quickly:
1. List part numbers, not just the part name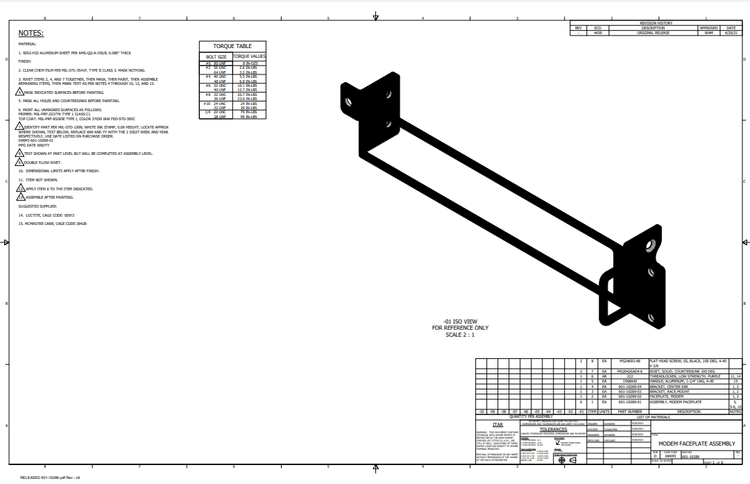
Part names are great, but it’s helpful to provide part numbers, too. A shop works on many projects simultaneously, and your custom metal fabrication could very well have the same (or similar) name as another one on the shop floor. Listing a number in addition to the name helps avoid any confusion.
We advise our customers to write the name of the part in the part description section and list actual digits (and/or letters) in the part number section.
The numbering and lettering system you use to label your custom metal fabrications is entirely up to you—there's no right amount of digits or required sequence of numbers and letters, so don’t stress about it too much.
2. Use the exact hardware name when possible
Your shop will want to know exactly what hardware you’re requesting for your custom metal fabrication. Like many companies, you may have internal part numbers and names for hardware that differ from standard naming conventions. The easiest way to minimize confusion and help your shop source the right hardware is to provide the name of the hardware manufacturer and the number they’ve assigned to the specific component.
Cross-referencing hardware numbers provided by customers is possible, but these systems take a little longer to work with. At our shop, we’re focused on getting customers precision sheet metal parts as fast as possible, and supplying the exact manufacturer information for hardware helps us make that happen.
3. Provide details for revision control
Whenever you need a revision, whether it's simply a wording adjustment or a critical geometry change, make a habit of documenting it. If revisions aren't flagged, sheet metal fabrication shops can miss critical requests, costing customers time and money.
There are different locations for revision notes on a print: the title block, the revision block, or both. If you write your revisions in both places, you’ll want to make sure that the information is identical in each space. If you work with us, we’ll always double-check revision notes and call you with any questions. But consistent documentation minimizes back and forth and helps our team expedite your project.
4. Include grain direction as needed
If your part requires a #4 stainless finish or a cosmetic finish, please indicate the grain direction on your print.
We default to the industry standard of going left to right across the print, but highlighting the preferred grain direction yourself guarantees that we’re on the same page.
5. Provide powder coat instructions
If you ask a shop to powder coat parts with no indication of the color, finish, or other details, you may not get exactly what you need. When possible, include the manufacturer and product number of the powder you’re looking for. If that's not possible, listing the color is a sufficient alternative.
If the color itself isn't a crucial requirement, you can simply specify your preferred type of finish. Specifying between matte, textured, smooth, gloss, and semi-gloss will help your shop narrow the options down.
What happens if you skip any of these steps? In a worst-case scenario, a sheet metal fabrication shop will make and deliver parts that don't meet your requirements. We can't speak for all metal fabricators, but we have policies in place at Approved Sheet Metal to prevent that from happening.
For example, we created a best practice to ensure revision control. Our team always starts a project from scratch rather than running a repeat order based on the current drawing set. Additionally, if we don't see enough information about finishing details, we'll call you to confirm color, texture, and sheen to ensure you're satisfied with the final result.
The more information you give us up front, the faster we can fabricate your parts. If you're unsure which details are required, we're happy to help. Just give us a call and ask—we want to get your project right the first time.
Digital File Formats & Model Sharing
In the modern era of precision sheet metal fabrication, clear and accurate communication between the design and fabrication teams is critical to the success of a project. Using the right digital file formats and sharing models efficiently can greatly enhance the fabrication process, reduce errors, and expedite production.
1. Importance of Standardized File Formats
To avoid confusion and ensure that all parties are working with the most accurate design, it’s essential to use industry-standard file formats. The most commonly accepted file formats for sheet metal fabrication include:
- DXF (Drawing Exchange Format): A widely used 2D vector file format for sheet metal cutting. It’s compatible with many laser cutting, punching, and CNC machining systems. DXF files allow for detailed geometric information, such as holes, cuts, and bends, to be transferred accurately to fabrication machines.
- STEP (.stp): A standardized format for 3D models that can be used across different CAD platforms. STEP files contain comprehensive data that allows the shop to understand not only part geometry but also design intent, which is especially important for complex assemblies or parts with multiple features.
- IGES (Initial Graphics Exchange Specification): Another 3D file format similar to STEP, IGES is used to transfer detailed surface data between different CAD systems. Though slightly less common than STEP, it’s still used in some engineering environments for sharing intricate designs.
- STL (Stereolithography): While typically used in 3D printing, STL files are occasionally shared for rapid prototyping or parts requiring complex geometries. Keep in mind that STL files represent surfaces, not solid bodies, and can lose some data in translation, so they are generally not preferred for high-precision fabrication work.
2. The Role of 3D CAD Models
Providing 3D CAD models alongside 2D drawings offers multiple advantages. Here’s why incorporating 3D models can optimize the fabrication process:
- Increased Precision: A 3D model provides more dimensional accuracy than a 2D drawing, especially when it comes to complex geometries or assemblies. This eliminates potential errors that could arise when interpreting 2D views alone.
- Design Validation: Sharing a 3D model allows fabricators to check the design for manufacturability. They can detect potential issues, such as sharp corners that may cause difficulty in forming or interference between components before the physical production begins.
- Collaborative Review: 3D models can be reviewed by multiple team members simultaneously, enabling more efficient feedback and reducing the back-and-forth that can occur with 2D drawings.
- Simulation and Testing: Some advanced sheet metal fabrication shops use 3D models to perform simulations, such as stress analysis, bend testing, and fit checks. This helps to identify any issues before fabrication, reducing costly mistakes and rework during production.
3. Annotations & Model Sharing
While providing 3D models is invaluable, it’s essential to ensure that these files are properly annotated. Annotations help clarify design intent and provide essential details such as:
- Dimensions: Specific measurements and tolerances for parts, holes, and bends should be clearly indicated in the model annotations.
- Material Specifications: Document the material type, grade, thickness, and surface treatment requirements directly within the CAD model to eliminate ambiguity.
- Assembly Instructions: If the part is part of a larger assembly, provide assembly constraints and orientation details to ensure proper fitment.
- File Sharing Platforms: With digital models, it’s important to use secure and efficient file-sharing platforms. Systems like Cloud-based CAD platforms (e.g., Autodesk Fusion 360, SolidWorks PDM, or Onshape) allow for real-time collaboration and version control, ensuring all team members have access to the latest model and that design iterations are tracked properly.
4. File Naming & Version Control
For efficient model sharing, always ensure your files are clearly named and versioned. Include details such as project or part numbers, revision status, and the date to avoid confusion. Adopting a naming convention and version control process will help prevent using outdated files and ensure smooth collaboration between teams.
By adopting these practices for file formats and model sharing, you can improve communication, speed up the fabrication process, and ultimately ensure that your precision sheet metal parts meet the exact specifications with reduced risk of error.
Are you ready to work with a precision sheet metal fabrication shop that values your time? Let's tackle your next project together. Submit a quote to get started!
Sheet Metal Fabrication Drawings FAQ
Listing part numbers helps avoid confusion and ensures that your custom metal fabrication project is accurately identified among multiple projects in the shop.
Providing the name of the hardware manufacturer and their assigned component number helps the shop source the right hardware quickly, minimizing confusion and accelerating the fabrication process.
Documenting revision details is essential to ensure that critical requests are not missed, saving time and avoiding additional costs. Consistent documentation helps expedite the project by minimizing back and forth communication.
Indicating the grain direction ensures alignment with your desired finish, such as #4 stainless or cosmetic finish. While the shop follows the industry standard by default, highlighting the preferred grain direction guarantees mutual understanding.
Including details such as the manufacturer, product number, or color preferences for powder coating allows the shop to meet your specific requirements accurately. Specifying the preferred type of finish further helps narrow down the options, ensuring satisfactory results.