Last updated on June 25th, 2024 at 12:21 pm
At Approved Sheet Metal, we're all about giving our customers the best possible experience and the highest quality custom fabrications. Sometimes, that involves making recommendations, or “upgrades”, to help our customers save time, save money, get better parts, or all of the above.
Each project is unique, but there are a few common upgrades we help customers make that improve the outcome of many of their projects. Let’s take a closer look at three of them.
Table of Contents
- 1 Upgrade Your Custom Fabrications to Optimize Cost and Lead Time
- 2 6 Tips for Designing Powder Coated Sheet Metal Parts
- 3 Optimize Cost and Lead Time for Custom Fabrications FAQ
- 3.0.1 Why should I consider using sheet metal instead of tubing for structural frames in my project?
- 3.0.2 What are the advantages of replacing welding with mechanical fasteners in custom fabrications?
- 3.0.3 When should I opt for powder coating instead of wet paint for finishing custom fabrications?
- 3.0.4 Will choosing mechanical fasteners over welding compromise the strength of my custom fabrications?
- 3.0.5 How does opting for powder coating enhance the durability of custom fabrications compared to wet paint?
Upgrade Your Custom Fabrications to Optimize Cost and Lead Time
1. Use sheet metal instead of tubing for structural frames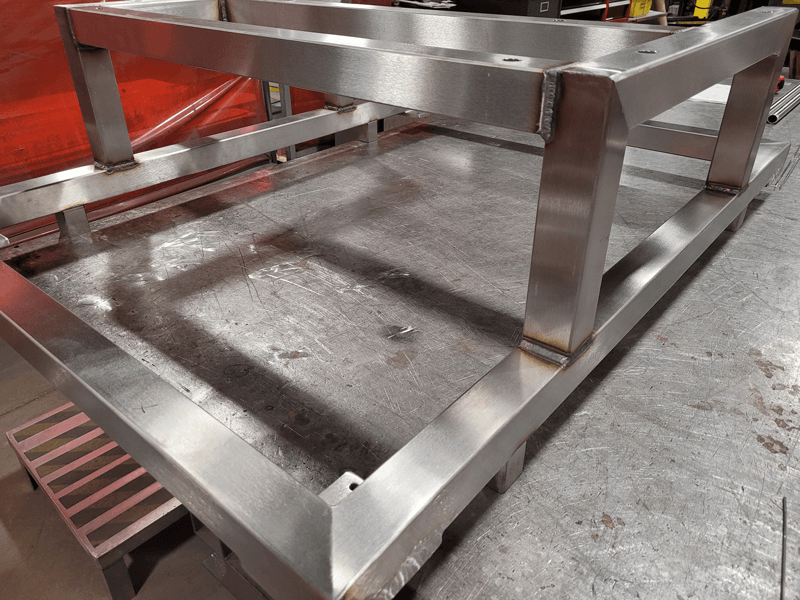
When customers need structural frames, they often assume that tubing should be the base for their projects. But tubing requires extensive saw cutting, an imprecise method that can compromise the quality of the frames.
A better option is to fabricate the frames from sheet metal instead of using tubing. In our shop, we can use our new high-power fiber laser to cut the frames and achieve greater precision. Laser cutting requires less labor than saw cutting, lowering costs and reducing lead times.
In terms of material sourcing, sheet metal is significantly more accessible than tubing, which means we can get your project started ASAP.
2. Replace welding with mechanical fasteners
Welding is a great option for many custom fabrications: it’s ideal for watertight applications or for achieving a smooth cosmetic appearance. But despite these advantages, fasteners like rivets and rivnuts are a preferable solution for many applications.
Rivnuts add load-bearing threads to thin sheet metal parts, allowing them to hold up to heavier external forces than welded parts could. And for applications like chassis, furniture, and bicycles, fasteners allow components to be routinely disassembled and reassembled. That’s simply not possible with welded parts.
3. Use powder coating instead of wet paint
Using wet paint to finish custom fabrications works well for specific applications, especially those requiring substantial corrosion resistance. However, in many cases, powder coating is the better option.
When we paint parts, we have to prime the surface, then wait for it to dry. Apply a coat of paint; wait for it to dry. And so on. Depending on the number of coats, a two-week wet paint job might take just one week with powder coating. Powder coating is also more durable than wet paint and less prone to cracking and shattering.
As you begin planning your next sheet metal fab project, consider making one or more of these upgrades. We’re always here to help advise on what’s best for your unique parts. Request a quote today!
Optimize Cost and Lead Time for Custom Fabrications FAQ
Sheet metal offers superior precision and quicker fabrication compared to tubing. Laser cutting with our high-power fiber laser allows for greater accuracy and reduced labor compared to saw cutting, resulting in cost savings and shorter lead times. Additionally, sheet metal is more readily available, allowing us to initiate your project faster.
While welding is suitable for certain applications, mechanical fasteners like rivets and rivnuts offer distinct advantages. Rivnuts enhance load-bearing capabilities for thin sheet metal parts and allow for disassembly and reassembly, which welded parts can't offer. Fasteners are ideal for applications requiring routine assembly adjustments.
Although wet paint is suitable for specific applications requiring substantial corrosion resistance, powder coating often proves superior. Powder coating significantly reduces drying times compared to the multiple coats needed in wet paint applications. It's more durable, less prone to cracking, and offers a faster turnaround, typically taking half the time of a wet paint job.
Not necessarily. Mechanical fasteners like rivets and rivnuts can enhance load-bearing capabilities in thin sheet metal parts, often exceeding the strength of welded joints. They offer a practical solution for various applications while maintaining structural integrity.
Powder coating not only reduces processing time but also offers superior durability compared to wet paint. It is less prone to cracking and shattering, making it an excellent choice for applications where longevity and resistance to wear and tear are crucial.