Table of Contents
- 1 Sheet metal fabrication for chassis, tanks, enclosures, and other sheet metal parts
- 2 Tolerance Stack-Up and Design for Manufacturability (DFM)
- 3 Sheet Metal Design for Manufacturing
- 4 Formed Sheet Metal Parts FAQ
- 4.0.1 What is the best method for forming deep boxes or U shapes in sheet metal?
- 4.0.2 What is back bending in sheet metal fabrication?
- 4.0.3 How can I ensure precision bends in my sheet metal parts?
- 4.0.4 What types of sheet metal dies are available for fabrication?
- 4.0.5 Where can I find a precision sheet metal shop for my fabrication needs?
Sheet metal fabrication for chassis, tanks, enclosures, and other sheet metal parts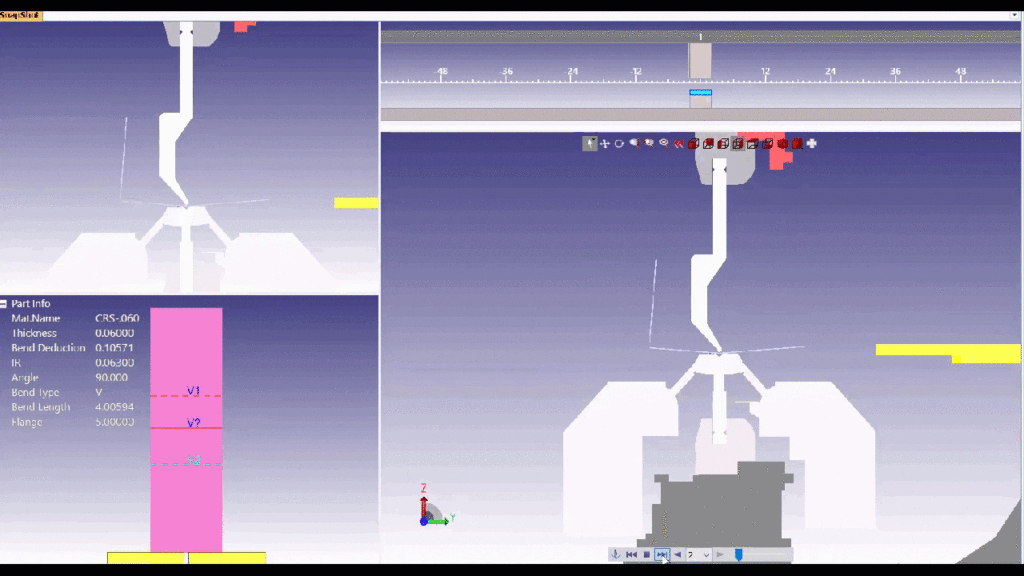
Last updated on March 11th, 2025 at 09:08 am
Forming deep boxes or U shapes in sheet metal isn’t as straightforward as it seems. Using a regular press brake to accomplish a complex bend often results in one of the metal legs twisting out of control—or crashing into the die itself. Instead of achieving a precision bend, the shape comes out contorted. And this is discovered by the fabricator on the shop floor resulting in lost material and time.
Solution 1: Back Bending
Some local shops may push back on the customer to change the design or jump to cutting the parts in multiple parts and then welding it back together. At ASM we have the talent and know-how to use an old school technique called back bending.
Back bending cuts the cost and gets your parts out fast. Basically, back bending achieves a deep U shape by first creating a W by adding a bend in the middle of the part, then flattening once the part has cleared any obstacles. It does work—if the design does not have any bend along this area. But even then, the process requires an experienced fabricator.
Solution 2: Software and Custom Sheet Metal Dies
To achieve a perfect complex bend every single time, forming software with precision sheet metal dies is the best solution.
Dies can be custom-made to cut and form a part according to the specified design. To create a deep U shape, for example, a “gooseneck” or “swan neck” die could be used to achieve the shape successfully.
At Approved Sheet Metal, our software can analyze the shape of your part to make sure we select the right die for the job. We have dies in many different shapes and sizes, and 90% of the time, we’ve already got the right die to match your project needs (the other 10% of the time, we’ll custom-order or come up with another solution to get the job done).
We have a wide range of sheet metal dies, including:
- Embossing Dies
- Punch Dies
- Cutting Dies
- Coining Dies
- Bending Dies
- Flanging Dies
Tolerance Stack-Up and Design for Manufacturability (DFM)
When designing precision sheet metal parts, understanding tolerance stack-up and design for manufacturability (DFM) is crucial to ensuring that the final assembled product meets specifications without costly rework or fitment issues.
Understanding Tolerance Stack-Up
Tolerance stack-up refers to the cumulative effect of individual part tolerances within an assembly. Informed design choices help prevent dimensional inaccuracies that could cause misalignment, interference, or assembly failures.
- Linear Tolerance Accumulation – Each bend introduces variation, and multiple bends in sequence can lead to greater deviations in the final part dimensions.
- Perpendicularity and Flatness Considerations – Improper tolerance control can lead to unwanted gaps or stress during assembly.
- Material Springback – Certain materials, like stainless steel and high-strength alloys, exhibit more springback, requiring compensation in the design stage.
DFM Strategies for Precision Sheet Metal Forming
To minimize manufacturing challenges and optimize cost-effectiveness, follow these best practices:
Use Realistic Tolerances
- Tight tolerances increase manufacturing costs and may require secondary processes like machining.
- Apply looser tolerances where possible and only tighten them in critical areas affecting function and assembly.
Standardize Bend Radii and Features
- Use common bend radii that align with available press brake dies to reduce setup time and tooling costs.
- Minimize complex or small-radius bends in thick materials to prevent cracking.
Consider Assembly Fit and Fastening Methods
- Allow for clearance holes and slots to accommodate tolerance variations in mating parts.
- Optimize fastener placement to prevent stress concentrations and distortion during assembly.
Control Flatness and Warping
- Large flat sections in thin materials may warp due to internal stresses.
- Introduce stiffening ribs or strategically placed bends to enhance rigidity.
Leverage GD&T (Geometric Dimensioning and Tolerancing)
- Use position tolerances instead of linear dimensions where appropriate to improve manufacturability.
- Apply datum structures to control critical features without over-constraining the design.
By proactively addressing tolerance stack-up and applying DFM principles, engineers can design parts that are not only manufacturable but also cost-effective and reliable in real-world applications. Would you like to include a case study or example to illustrate these principles further?
Formed Sheet Metal Parts FAQ
The best method for forming deep boxes or U shapes in sheet metal is to use precision sheet metal dies with forming software. This ensures a perfect complex bend every time.
Back bending is an old school technique used in sheet metal fabrication to achieve a deep U shape. It involves creating a W shape by adding a bend in the middle of the part and then flattening it once the obstacles are cleared. However, this method requires an experienced fabricator and may not be suitable for designs with bends along the back bending area.
To ensure precision bends in sheet metal parts, using custom sheet metal dies with forming software is recommended. These dies can be specifically designed and cut according to the desired shape, such as a deep U shape, using dies like "gooseneck" or "swan neck." Analyzing the part's shape and selecting the right die through software helps achieve consistent and accurate bends.
Approved Sheet Metal offers a wide range of sheet metal dies, including embossing dies, punch dies, cutting dies, coining dies, bending dies, and flanging dies. These dies come in various shapes and sizes, ensuring versatility and compatibility with different project needs.
If you're looking for a local precision sheet metal shop in Hudson, New Hampshire, you can request a quote from Approved Sheet Metal. They have the expertise and a wide range of sheet metal dies to ensure your projects are completed with precision and efficiency.